TEGS Thai Environmental German Services
We specialize in Industrial Cleaning. We help you clean up all the waste and make sure to leave a pristine work site.
Follow us on Facebook
Thai Environmental German Services Co., Ltd
1/6 Banlang Rd., Tambol Hueypong, Amphur Muang, Rayong Province 21150
033 012 645
[email protected]
Office Hours
Mon-Sat 08:00-17:00
Our ISO certification is proof that you can trust us!
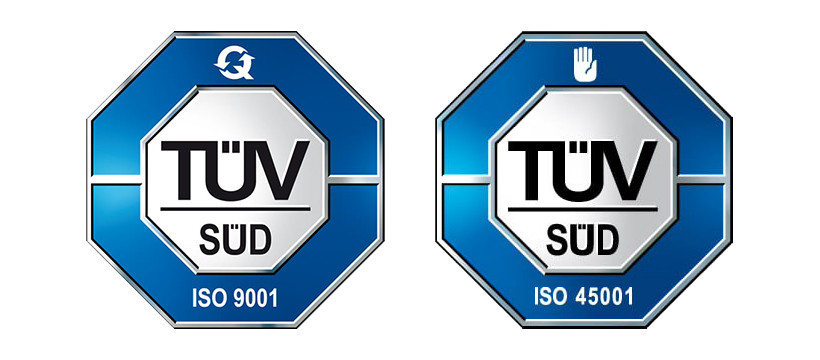
Nothing Found
Sorry, no posts matched your criteria